Корпуса
| |
kimsos | Дата: Вторник, 14.12.2010, 22:01 | Сообщение # 1 |
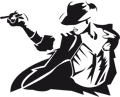 Главнокомандующий
Группа: Администраторы
Сообщений: 396
Статус: Offline
| Автор: Билозор Юрий Васильевич (aka YOOREE) Напишу немного по корпусам/оформлению, как обещал. Материал этот - называется вспененный ПВХ, используется в конторах, которые специализируются на изготовлении вывесок, лайт-боксов, стендов и прочей наружной рекламы. Этот пластик бывает разной толщины, примерно от 0,5 мм. до 12 мм. толщиной, он относительно легкий, достаточно прочный и вполне легко режется острым канцелярским ножом под металлическую линейку. Я обычно использую тот, что толщиной 3 или 4 мм. Панели, естественно надо резать под углом 90град. Затем панели склеиваются между собой, тут несколько разных способов можно придумать. Я чем дольше делаю, тем больше совершенствуюсь уже приноровился делать переднюю и заднюю панель съемными - очень удобно. Склейку произвожу немецким клеем Cosmofen CA-12, он напоминает суперклей для обуви - прозрачный и очень цепкий. По-идее, можно и альтернативные типы клея подыскать. Для оклейки корпусов использую самоклеющуюся пленку фирмы ORACAL, любимый тип - черная, матовая. Надписи (буквочки) высотой 3-4 мм. вырезаются из той же пленки золотистого цвета и потом переносятся на переднюю панель с помощью специальной монтажной ленты/пленки, часто называют просто монтажкой. Она полупрозрачная из-за того что покрыта липким слоем. Но липкость его слабее чем липкость слоя на обратной стороне пленки ORACAL. Перед наклейкой букв следует выбрать (с пом. кончика остой иглы или ножа) промежутки между буквами/надписями и внутри букв. И потом приложить монтажку к поверхности букв и прижать. Даже не просто прижать, а притереть. Ногтями часто притирают, например. Так что бы монтажка плотно приклеилась. Потом внимательно и не спеша отводим край ленты добиваясь того чтобы буквы оставались на монтажке и отошли от глянцевой подложки ORACAL. Если некоторые буквы отходят неохотно, надо вернуться и еще притереть их ногтями к монтажке. Особенно края букв. Если буквы мелкие, то иногда поступают так – выбирают только промежутки между букв и клеят надпись на панель. А позже выбирают промежутки внутри букв. На некоторых монтажках встречается разметка. Разметка позволяет наклеивать надписи ровно, не производя разметочные линии на панели. По линиям можно на глаз судить ровность расположения наклеиваемой надписи по горизонтали. Учтите что разметочные линии выполненные (если будете их выполнять) маркером/карандашом и т.п. оставляют след который практически невозможно удалить. Поэтому лучше не чертить их вообще. Но у клейщика должны быть острый глаз и твердые руки. Буквы мне рисовали в Corel Draw .Потом, файл с компьютера отправляют на плоттер - этакий станок с острым вращающимся ножом и он делает прорези на пленке. Только очень хорошие плоттеры могут аккуратно вырезать мелкие буквы. У нас в городе я знаю только один такой плоттер. В других фирмах плоттеры проще. Суммируя выше изложенное - и пластик и пленку и клей ( а возможно и хороший плоттер) можно найти в какой-нибудь фирме в вашем городе занимающейся рекламой.
Лучше вбитый шуруп, чем вкрученный гвоздь...
|
|
| |
kimsos | Дата: Вторник, 14.12.2010, 22:01 | Сообщение # 2 |
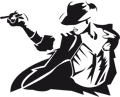 Главнокомандующий
Группа: Администраторы
Сообщений: 396
Статус: Offline
| Обработка вспененного ПВХ Статья об обработке данного материала. Так сказать, рекомендации производителя... Многие радиолюбители применяют данный материал при изготовлении корпусов своих конструкций. Ну а я выложу некоторые виды обработки ПВХ. Вспененные поливинилхлоридные (ПВХ) листы представляют собой идеальный материал для рекламы, строительства и промышленных нужд, как внутри, так и вне помещений. Листы вспененного ПВХ легки и прочны; поверхность листов обладает универсальными свойствами: на нее можно наносить краску и печатать изображения, ее можно штамповать, гравировать и фрезеровать, в зависимости от желания потребителя. Распиловка вспененного ПВХ Вспененный ПВХ можно пилить ручной, дисковой, ленточной пилой и лобзиком. Хорошие результаты дают ручные пилы, предназначенные для работы по дереву. Пилы, предназначенные для работы по металлу, из-за мелкого шага зубов могут забиваться. Лучшее качество достигается при скорости пиления до 300 м/мин и при подаче около 30м/мин. Рекомендуются следующие значения углов: а = 5 - 10° - передний угол зуба, g = 10 - 20° - задний угол шаг зубьев 5 – 10 мм Сверление вспененного ПВХ Вспененный ПВХ можно сверлить стандартными дрелями, предназначенными для металла. Лучшее качество достигается при 50 – 300 об/мин и подаче 3,5 – 6 м/мин. Рекомендуются следующие значения углов: ф = 100 - 110° угол при вершине; b = 30° - угол подъема; a =0-5 0 - передний угол Фрезерование вспененного ПВХ Вспененный ПВХ легко обрабатывать на стандартных универсальных вертикальных или горизонтальных фрезерных станках. Чтобы предотвратить повреждения поверхности, при фиксации необходимы деревянные или пластиковые прокладки. Рекомендуемый режим фрезерования: Скорость резки: около 900 м/мин Подача: 0,3 – 0,6 м/мин a = 5 - 20°- передний угол; y = 10-25° задний угол Обработка краев Край может быть окончательно обработан рубанком, наждачной бумагой или опиливанием при помощи стандартного оборудования по дереву или пластику. Когда материал находится под постоянными динамическими нагрузками, неровные срезы могут привести к образованию трещин и разломов. Листы вспененного ПВХ толщиной до 3мм, можно легко резать ножом. Штамповка вспененного ПВХ Качество штамповки определяют следующие факторы: толщина листа, температура листа, оснащение для штамповки, а также угол резания лезвия. Листы толщиной 2 и 3 мм штампуется легко. Однако, при правильном оборудовании и правильных методах, простые формы можно штамповать из листов толщиной от 4 до 6мм. При этом края резки будут слегка закруглены. Качество штамповки может быть улучшено с помощью небольшого подогрева листа. Подходят инструменты для штамповки картона или других вспененных материалов. При штамповке вспененного ПВХ крайне важно, чтобы лезвия были скошены на 30°. Горячая гибка вспененного ПВХ В принципе можно использовать любое стандартное оборудование для гибки термопластиков. Зачастую предпочтительно оборудование для гибки, сделанное самим пользователем. Равномерная температура и предварительно определенная зона постоянного нагревания – это важные условия для аккуратной гибки. Лучшая температура гибки для, например, для Forex от 115-130°С. Если температура слишком высокая, есть опасность появления трещин и расколов ячеистой структуры, в частности это относится к более толстым листам. При температурах ниже 115°С материал будет подвергаться большому напряжению и, скорее всего, вернется к своему первоначальному виду. Для вспененных материалов односторонний нагрев будет иметь успех до определенной степени и гибка не всегда будет визуально удовлетворительна. В таких случаях помогает V-образный разрез на внутренней стороне гибки. Во всех случаях радиус гибки должен превышать 1,5–2 толщины материала, в частности, когда требуется визуально удовлетворительная гибка. Важно, чтобы изделие, которое было согнуто, оставалось зафиксированным в таком положении, пока не остынет. Склеивание вспененного ПВХ Для склеивания листов вспененного ПВХ между собой больше всего подходит растворяющий клей (для так называемой холодной сварки Cosmofen Plus), в некоторых случаях используется реактивный клей (например, так называемый секундный клей, Cosmoplast 507, 500L, Cosmofen CA 12). При склеивании с другими, непористыми или неабсорбирующими материалами, можно использовать, прежде всего, растворяющий контактный клей ( клей должен наноситься на обе поверхности, приблизительное количество 150 г/м?) или двухкомпонентный полиуретановый клей без растворителей (наносится на одну поверхность). Для склеивания с пористыми или абсорбирующими материалами можно наряду с вышеуказанным контактным клеем использовать водный дисперсный клей или двухкомпонентный полиуретановый клей. Рекомендуется проводить собственные пробы в каждом конкретном случае. СОВЕТ. Наряду с комбинированием материалов при выборе клея следует обращать внимание на другие факторы, которые также могут повлиять на результаты склеивания, например устойчивость к атмосферным воздействиям, к химическим веществам, эластичность клеевого шва и т.д. Сварка вспененного ПВХ струей горячего воздуха При сварке вспененного ПВХ струей горячего воздуха соблюдаются те же критерии, что и для других термопластиков, то есть подготовка сварного шва и выбор правильной температуры сварки. Существенным является равномерное нагревание, следует избегать локального перегрева. Можно использовать стандартный сварочный пруток, как для листового ПВХ. Для того, чтобы избежать перегревания листов, сварочный пруток должен быть предварительно нагрет до 70 - 80°С. Рекомендуемые параметры работы: Края швов скошены до: 60° Температура сварки: 280 - 290° С Скорость сварки: приблизительно 3.5м/мин (скоростная сварочная насадка) Термоформовка вспененного ПВХ Вспененный ПВХ, может подвергаться термоформованию вакуумной формовкой. Однако, следует учитывать, что Вспененный ПВХ представляет собой двухфазовую систему, 50% объема которой составляет заключенный внутри воздух. Эта система позволяет даже при температуре формования сохранять эластичность. В отношении возможности формования, растяжимости и четкости изображения детали необходимо принять некоторые ограничения. Воздух, заключенный в закрытых ячейках, как эластичный компонент не может пластифицироваться под влиянием нагревания. Это ведет к более легкому формованию и растягиванию листа. Следует избегать острых краев и углов. Радиус должен составлять не меньше, чем 2 толщины листа. Также следует избегать небольших выпуклостей, углублений, рифленых участков, ребер и т. д., что является следствием сильного растяжения материала. В зависимости от намеченной пропорции вытяжки рекомендуется, чтобы боковые стены изделия конструировались с углом наклона от 5 до 8°. Чем больший угол выбран, тем лучше пропорция вытяжки (высота изделия h к диаметру или минимальной ширине d). Уже достигнуты пропорции между 1:1 и 1:1,25. Пропорции вытяжки h : d , превосходящие 1:1, возможны, но тогда необходим подходящий дизайн формы. Для вспененного ПВХ возможны два различных температурных диапазона формования. Термоэластичный диапазон 115-130°С. В этом диапазоне материал показывает хорошую растяжимость, но иногда может с трудом поддаваться формованию. Чтобы компенсировать тепловую емкость материала, рекомендуемый нагрев чуть выше температуры формования. Термопластичный диапазон 160-170°С Растяжимость материала в этом диапазоне немного меньше, чем в термоэластичном диапазоне, но он легче формуются, Небольшое последующее расширение листа приводит к более или менее зернистой поверхности. Важен контроль точности температуры, т.к. при превышении 180 ° С наступает тепловое разложение материала. Для более толстых листов, скажем более 3мм, настоятельно рекомендуется двухсторонний нагрев. Время разогрева, указанное в таблицах, должно рассматриваться только в качестве руководства. Оно предназначено для использования с оборудованием, оснащенным предусмотренным лучистым нагревателем. Время нагрева при одностороннем нагревании керамическими нагревательными приборами. Мощность нагревателя 20 кВт/м2 Температура 450°С | Толщина листа в мм | 2 3 4 5 6 | Нагревательный цикл в сек. | 40 60 80 110 140 – 150 | Время нагрева при двухстороннем нагревании (типа "сэндвич”) керамическими нагревательными приборами. Мощность нагревателей: верхний 20кВт/м2, нижний 20кВт/м2 Температура нагревателей: верхний 450°С нижний 380°С | Толщина листа в мм | 2 3 4 5 6 | Нагревательный цикл в сек | 10 – 25 25 – 35 45 60 80 | Способность вспененных материалов удерживать тепло ниже, чем у сплошных материалов той же толщины. Поэтому необходима адекватная температура формы, чтобы избежать охлаждения в начале цикла формования. Растяжение листов вспененного ПВХ лучше при низкой интенсивности растягивания. Поэтому вакуум должен подводиться постепенно, а не сразу в полную силу. В завершении формования требуется полный вакуум. Окраска вспененного ПВХ Во многих применениях желательно использовать цветные листы PALIGHT. Цвет легко изменить, применив краску. Краски, нанесенные на PALIGHT хорошо держатся. В зависимости от типа краски и метода нанесения можно достичь глянцевой или атласной поверхности, а также возможны металлические тона и эффекты структуры. Наиболее подходящими для окрашивания PALIGHT являются следующие типы: • ПВХ, • Акриловые, • Двухкомпонентные полиуретановые В основном, грязь и пятна могут быть удалены с PALIGHT без затруднений. Одним исключением являются пятна, оставленные растворителями. Для удаления пыли и грязи, которая растворяется в воде, можно использовать мыльную или простую воду Надписи, сделанные некоторыми фломастерами, через какое-то время не могут быть полностью удалены. Для снятия электростатического заряда необходимо использовать антистатики, которые рекомендуются производителями красок, так как не все антистатические вещества совместимы со всеми красками и красками для шелкографии. Опыт показал, что в некоторых случаях нанесение краски приводит к уменьшению ударопрочности листа. Это отчасти верно для красок, содержащих агрессивные растворители, или для тех красок, которые становятся хрупкими при высыхании. Трафаретная печать вспененного ПВХ На листы вспененного ПВХ очень хорошо наносится печать методом шелкографии обычными красками для твердого ПВХ, так, например: производитель Marabuwerke - Maraplast D ; Maragloss GO + GN ; MaraspeedSL ; Maraprint SP ; Marastar SR ; Marasoft MS ; Libragloss LIG . Производтель Sericol GmbH- XG-043 MJ-168 PY-284 MV-205 Установка вспененного ПВХ При установке обязательно надо учитывать коэффициент линейного расширения вспененного ПВХ. Это означает, что требуется делать овальные отверстия для возможной деформации листов при значительных размерах вывески и перепадах температур.
Лучше вбитый шуруп, чем вкрученный гвоздь...
|
|
| |
kimsos | Дата: Вторник, 14.12.2010, 23:06 | Сообщение # 3 |
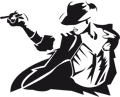 Главнокомандующий
Группа: Администраторы
Сообщений: 396
Статус: Offline
| Проектирование корпусов В свое время проходил "срочную" службу и меня, как "рабсилу", закинули в НИТИ, а собственно в КБ. Задача моя была рисовать и собирать корпуса для аппаратуры. В то время внешнему виду уделяли мало внимания, но с технической стороны относились к этому вопросу очень критично. Вкратце основные принципы создания корпусов, в порядке приоритетов:
1. Хорошая экранировка между блоков и защита от их взаимодействия 2. Минимальное использования пространства(только для опытных образцов) 3. Легкость и максимальная разборность на составные 4. Максимальная прочность(обратите внимание, даже при советской власти это не было основным), максимально жесткое крепление внутренних блоков 5. Правильное расположение центра тяжести 6. Симетричность и простота внешнего вида.
А теперь подробней...
Макетирование и замерыВ первую очередь надо спроектировать само устройство. Затем уже проектировать и сам корпус. Для простоты можно сделать картонные шаблоны в виде коробочек, где основанием будет размер ПП, а высотой размер самого большего элемента. Затем надо расположить все блоки на бумаге, с максимальной рациональностью(не забывая правила: все для питания в одном месте, усилители в другом, пред. усилители в третьем и т.д., не забывая про то что соединительные кабели должны быть максимально короткими) на расстоянии 10- 20 мм. Теперь отмечаем расположение блоков на углах и не забывайте про растояние между ними. Самый высокий блок будет определять высоту корпуса.
Выбор материала и геометрииСледующий вопрос встает за выбором материала и собственно расчетов геометрии. После выбора материала замеряем его толщину и начинае проверять все на бумаге, чтоб не получилось: "считал, считал, собрал, начал ставить все на места, не лезет" crying . Делаем макет корпуса из бумаги и проверяем, а влезет ли туда Ваша схема, помните, что высота корпуса должна быть больше самого высокого блока! Когда у Вас будет достаточно опыта, этот шаг можно будет и упразднить winked Не поленитесь проверить на макете с уже готовыми платами!
Теперь о выборе материала, тут Вам никто не советник! Всегда рассчитывайте свои силы и финансы в трезвой памяти и здравом рассудке!
ЭкранировкаТехническая часть этого вопроса проста, если корпус и перегородки между блоками из метала, НО! вдруг пришлось делать из дерева, пластмассы, эпоксидной смолы и прочего? Как вариант, можно обклеить стенки корпуса, с внутренней стороны, фольгой (можно пищевой, но лучше толщиной примерно в 0.5мм, такую найти очень легко и дешево стоит), металлической сеткой, сеткой для чистки паяльника и т.д.
Если вы делаете корпус при помощи эпоксидной смолы, то экран можно уложить "пирогом", т.е. в форму закладывается первый слой основного материала(лучше стекловолокно), мелкая металлическая сетка и опять основной материал. Главное, чтобы экранирующий материал имел контакт с экраном других стенок и выводом в одной точке, которая подключается к земле или экранирующему выводу трансформатора (обычно есть на торах)
ПлоскостиСам корпус я предлагаю делать из плоских составных, для этого потребуется сделать каркас. Сам раньше делал из старого "железного конструктора", очень удобно, а в целом получается еще и прочно! Легко манипулировать с перегородками. Если нет под рукой, можно сделать из брусьев дерева, пластмассы, фольгированного стеклотекстолита и т.д. При всех этих действиях не забывайте о внешнем виде! Лицевая сторона должна быть по высоте и ширине самого корпуса, а верхняя и нижняя часть поверх боковых сторон. Для создания внутренних отсеков, так же потребуется создание каркасов, желательно чтоб они держались на основном. Для облегчения ремонта аппарата, все платы должны крепится к каркасу, тогда не нужно разбирать весь агрегат, чтоб осмотреть платы и детальки.О центре тяжестиДля того чтоб центр тяжести был по центру, тяжелые части предлагаю располагать как можно ближе к середине, а радиаторы (если их несколько) по бокам.
Внешний видПожалуй, для многих он был бы и важнее всего раньше сказанного, но уделяю этому меньшую часть, творчество еще никому не помешало! wink Однако укажу главное правило, по которому делаю корпуса я. Для начала взглянем на рисунок:
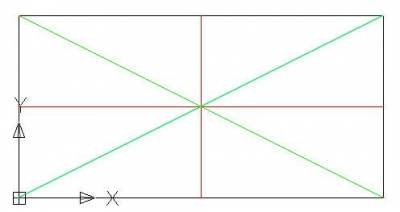 Красным нарисованы линии симметрии, зеленым диагональные линии, которые в основном и используют для размещения блоков регулировок. От центра рисуется круг, радиусом с четверть ширины корпуса и в местах пересечения с зеленой линией, я и располагаю какие либо объекты, в верхних углах обычно кнопка включения и индикация, в нижних входы и выходы. Этот способ у нас называли "принцип золотого сечения", я к нему привык и использую до сих пор.
P.S.Сам я пользуюсь этим методом и на проектирование у меня уходит около 30-60 минут. Делаю корпуса в основном из эпоксидной смолы и метала. Каркас для металлического корпуса из арматуры, квадратного сечения, соединяя путем точечной сварки. Для корпусов из эпоксидной смолы каркас не выполняю, а загибаю края (на формочке) и соединяю болтами, внутренние перегородки выполняются вместе с дном, путем подвешивания материала и частичного вложения в средний слой дна).
Лучше вбитый шуруп, чем вкрученный гвоздь...
|
|
| |
kimsos | Дата: Вторник, 04.01.2011, 16:13 | Сообщение # 4 |
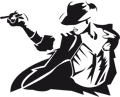 Главнокомандующий
Группа: Администраторы
Сообщений: 396
Статус: Offline
| Самодельные корпуса из подручных материалов Корпус для зарядки... Сама зарядка: Оргстекло было взято из подкасетника для дисков на 5 штук (сразу не сфоткал, а потом поздно было может позже куплю и размещу из чего делал) Черновой вариант: Т.е. вырезал, шлифанул торцы, склеил Клеил сначало ДИХЛОРЭТАНОМ, а потом плюнул (долго ждать) - СУПЕР МОМЕНТОМ (на основе цыанакрилата) - СЕКУНДНЫЙ что Схватывает быстро, держит крепко. Далее шлифовка. Прошёл плоскости - посбивал выступающие части. Корпус получился из двух частей (сам корпус и крышка к нему): Соединяются обе части втулкой с резьбой и двумя винтами (такие используют для ручек межкомнатных дверей). Крышка сделана из двух частей, одна из которых, вставляется во внутрь. Вторая ложится на торец корпуса - обеспечивая тем самым невозможность смещения или проворота... Примерка: По кройке корпуса - получилась продольная щель - решил её не заделывать - вентиляция. В низу насверлил отверстий, чтоб воздух мог конвектировать (перемешиваться) обеспечивая, тем самым, вентиляцию В собранном виде: Далее врезал разъём воходного питания. Покраска - автоэмалью, чёрной, матовой, в несколько слоёв, по граням с верху: Дунул чуток на радиатор, чтоб не скалил зубы оранжевым цветом Сборка: В собранном виде, в работе: Время изготовленя 5 часов. Заряжает быстро качественно (до полного заряда - ждать приходится подольше - под занавес ток идёт маленький, зато не будет перезаряда). Спасибо СЛАВОНУ, за схему, плату и разработку... 
Лучше вбитый шуруп, чем вкрученный гвоздь...
|
|
| |
kimsos | Дата: Среда, 26.01.2011, 22:57 | Сообщение # 5 |
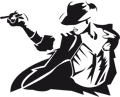 Главнокомандующий
Группа: Администраторы
Сообщений: 396
Статус: Offline
| Изготовление лицевой панели Нравится коробочка? Хочешь научу делать такие же? Тык под кат! Коробка. Корпус покупается готовый. Стоит он в пределах ста рублей, так что не стоит возни. Зато сразу будет красиво. Вот этот корпус я вообще намутил нахаляву, выцыганив сэмплом у компании Pac-Tec Разметка Короче, для начала прикидываешь где у тебя что вылезет. Светодиоды, кнопки, экран и прочая фигня. Проще всего это сделать намазав их чем нибудь и приложив крышку. Я обычно мажу капельками флюса, но ты можешь применить и математические построения. Далее в крышке вырезаешь дырки. Особо стараться нужно только для всяких светодиодов и прочих конструкций которые будут держаться за крышку. Для кнопок же можно и нужно профигачить дыры побольше. Как видишь, я не церемонился особо. Кнопки Их нужно взять такие, чтобы нажимная часть была заподлицо с верхней крышкой, ну или выступала на треть миллиметра, не больше. Регулируется шайбочками подкладываемыми под крепеж платы. Мы будем делать клаву типа мембранной, поэтому ход клавиш будет мизерный. Морда Рисуем морду, вот тут желательно как можно более точно попасть в размеры. Т.к. от качества отрисовки будет зависеть как внешний вид, так и удобство пользования. Печатаем ее на бумаге, лучше на плотной. Я напечатал на той же фотобумаге на которой штампую заготовки под ЛУТ. Сверху бумаги накатываем прозрачную самоклеящуюся пленку. Лучше в два три слоя. Можно скотч, но он тонкий и редко бывает нужной ширины. Края пленки заворачиваем на другую сторону и там приклеиваем. Дырку от экрана LCD я надрезал на манер почтового конверта, а лепестки завернул на другую сторону. Под кнопки наклеил несколько слоев изоленты - она будет служить усиливающим элементом, чтобы не прорвались кнопки. Также не помешает либо вокруг окна LCD либо прям поверх, защитным стеклом, приклеить лист тонкого прозрачного пластика (как от ПЭТ бутылок, только прямой. Пластины такого пластика обычно вставляют в воротник новых рубашек), на тот же двусторонний скотч. Чтобы, во-первых, защитить экран. Во-вторых, укрепить края дырки иначе случайным движением их можно порвать. У меня края лежат прям на морде дисплея, поэтому я ставить ничего не стал. Финал Ну, а потом все лепится на двусторонний скотч. Жутко липкая гадина, поэтому вначале лепишь скотч на корпус, а потом, в одно движение, налепляешь морду. Разглаживаешь и собираешь. Битте!
Лучше вбитый шуруп, чем вкрученный гвоздь...
|
|
| |
kimsos | Дата: Понедельник, 28.03.2011, 19:00 | Сообщение # 6 |
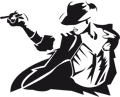 Главнокомандующий
Группа: Администраторы
Сообщений: 396
Статус: Offline
| Автор: rubenlukin Материал взят с форума сайта DIY-audio Подсветка ручек Ещё вчера собрал наконец-то усилитель для саба (собственно саб чуть раньше), подключил весь комплект (целых 2.1!!!). Сутки прогона - полёт нормальный! Сверхъяркие зеленые светодиоды приклеены суперклеем к кусочку текстолита, а тот, в свою очередь, к передней панели: В передней панели большое отверстие: Крутилка покупная, сзади вставлен кусок картона с наклеенной алюминиевой фольгой: Поначалу пробовал с красными, тоже симпатично, потом спалил их, экспериментируя с параллельным подключением. В итоге пришел к такой схеме: ЛМ-ку можно маленькую ставить, в ТО92 но это если напряжение поменьше. У меня большая уже была прикручена к радиатору, подстроечник присобачен, так что переделывать не стал.
Лучше вбитый шуруп, чем вкрученный гвоздь...
|
|
| |
kimsos | Дата: Среда, 13.04.2011, 16:27 | Сообщение # 7 |
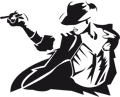 Главнокомандующий
Группа: Администраторы
Сообщений: 396
Статус: Offline
| Первый блин... корпус Первая попытка уйти от конструкции в картонной коробке Просто ящик с просто чертежом. Сложности с железками. Вентиляция Несерьезная шпатлевка После окраски Крутилки и разъемы
Лучше вбитый шуруп, чем вкрученный гвоздь...
|
|
| |
kimsos | Дата: Понедельник, 18.04.2011, 15:07 | Сообщение # 8 |
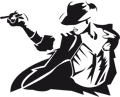 Главнокомандующий
Группа: Администраторы
Сообщений: 396
Статус: Offline
| Еще один пример изготовления корпуса из вспененного ПВХ Те кто будет использовать этот материал для изготовления придумают свою технологию, пластик очень пластичен. Имеет разную толщину, я использовал 3мм. и 6мм. Пластик можно купить в рекламных агенствах, если у них есть обрезки могут отдать так. Там же можно купить клей (пригодится в хозяйстве), клеет практически все и мгновенно, пальцы тоже. Вот это клей. От линий сгиба проводим на расстоянии 1 мм. еще линии с обеих сторон. Примерно под углом 45 % вырезаем ножом канавку. Канавки нагреваем (лучше феном, от зажигалки копоть остается, что, в общем не критично). Делаем днище (толщина пластика 6 мм.) .Бортики приклеиваем, в них сквозь верхний кожух будем вкручивать шурупы. Клей: цианоакрилатный клей COSMOFEN CA 12 Цианоакрилатный клей (опасно - цианистый акрилат. Склеивает кожу и веки глаз за несколько секунд). Это на подобие супер клея (такие маленькие тюбики, в основном китайского происхождения), только как бы качественнее. Были случаи на работе когда по не осторожности клей попадал в глаза. За несколько секунд клей в глазу кристаллизуется и очень больно режет глаз. Возили к глазному хирургу. Клеить надо осторожно. повернуть деталь уже не получится, схватывает сразу, особенно ПВХ. ТЕХНИЧЕСКИЕ ХАРАКТЕРИСТИКИ КЛЕЯ Cosmofen Фирма WEISS клей Cosmofen Универсальный однокомпонентный клей низкой вязкости (70 мПа/с) мгновенного действия на основе цианакрилата. Клей хорошо переносит воздействие низкой и высокой температуры, а также влияние неблагоприятных погодных условий. Клей поставляется в полиэтиленовых флаконах ёмкостью 20 г. (20 штук в упаковке) и 50 г. (10 штук в упаковке). Применение: Предназначен для склеивания пластмасс, стекла, резиновых изделий, баннерных тканей из ПВХ, жестких ПВХ изделий. Используется в оконном производстве для приклеивания уплотнителей к оконным рамам, алюминиевого профиля к оконному профилю из ПВХ. COSMOFEN CA12 -однокомпонентный клей моментального действия для приминения в промышленности и в быту, с высокой начальной адгезией к самым разнообразным материалам. Прежде всего расчитан на склеивание резиновых, пластиковых и поверхностей, часто применяется для склеивания уплотнительных профилей, торцевых срезов и приклеивания уплотнителей к профилям из ПВХ и аллюминия. Применяется также для склеивания виниловых такней, изделий из кожи металла и стекла. Использование Склеиваемые поверхности очистить предварительно от грязи, жира, влаги и прочего загрязнения при помощи очистителя . Ткань, используемая для очистки, не должна иметь жесткий ворс можно использовать цветную ткань. Применяется также для склеивания винилловых тканей, изделий из кожи, стекла и металла. Хранение Срок хранения 6 месяцев, при t=+6 С - 12 месяцев. Меры предосторожности COSMOFEN CA12 - Xi (опасен для здоровья)! Оригинал на сайте Электроника студийных вспышек.
Лучше вбитый шуруп, чем вкрученный гвоздь...
|
|
| |
|